Introduction to mCom ONE
Machine builders, system integrators and operators must manage safety proactively to achieve zero downtime and prevent hazards. With reports being sent back and forth between these stakeholders, it can be difficult to accurately track progress, document measures and derive valuable learnings from data.
Looking ahead, the Industrial Internet of Things (IIoT) will facilitate new concepts for more efficient production, including adaptive configurations and digital twin technologies. In the world of IIoT, machinery safety compliance will require a dynamic solution for management of hazards in a life-cycle perspective.
What is mCom ONE?
To meet current and future machinery safety compliance and risk management needs, TÜV SÜD has developed the cloud-based software solution mCom ONE. The tool facilitates life-cycle management of hazards by bringing machinery, people and processes together while keeping the data readily available for stakeholders across sites.
By seamlessly integrating machines and infrastructure, from design right through to commissioning and operation, mCom ONE streamlines processes across the supply chain. A user-friendly checklist guides you through the compliance process and can be tailored to your requirements, while a final report generates a prioritised action list for any areas of non-compliance.
mCom ONE is designed to facilitate the effective detection and elimination of hazards that pose a threat to business continuity, and it includes hazard pools for efficient and consistent assessments.
Application mCom ONE supports engineers in following a checklist-based audit to identify non-compliance points (hazards) to the EU machinery safety directive and national machinery safety standards. The reports created are the basis for CE marking of machines as required by EU legislation.
Following diagram describes features available in mCom ONE application.
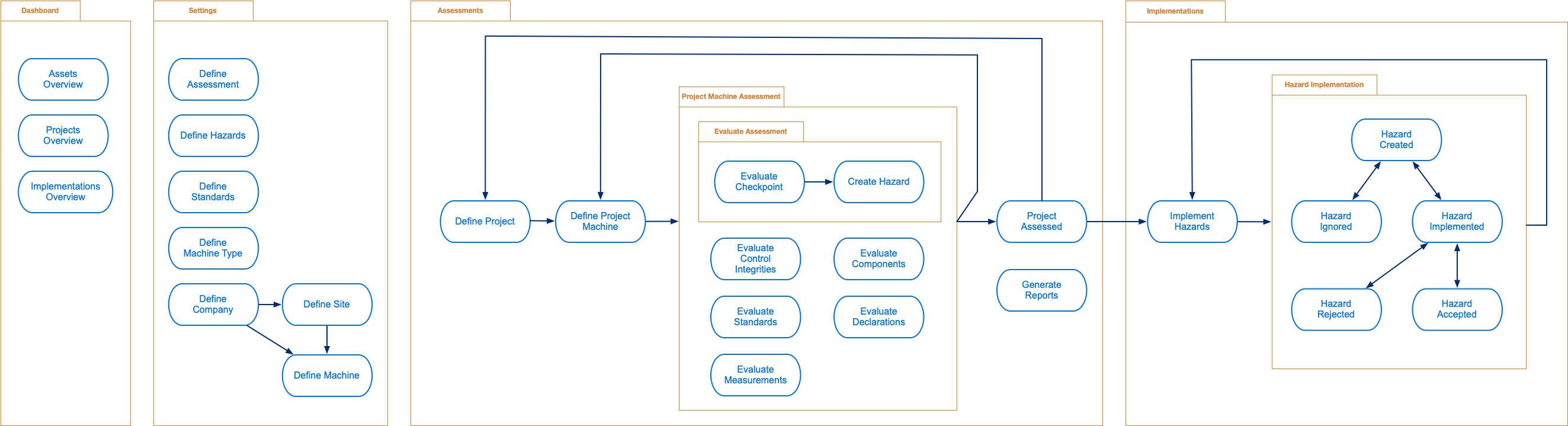
Features in mCom ONE
Why are streamlined assessments important?
Machinery safety plays an important role when it comes to the overall performance of any manufacturing company. To ensure business continuity and enhance safety levels, safety compliance needs to be managed proactively and effectively across sites. This can prove a complex task as manufacturers are faced with a range of domain and market-specific requirements. The diversity of safety hazards adds another layer to the intricacy of risk management in industrial manufacturing. Streamlined and transparent safety assessment processes will help you to effectively reduce risk across your organisation.
Adaptive configurations are introducing a new dimension to machinery safety, as hazards are changing in accordance with the shifting set-up. Consequently, all plug & play concepts require a machine life-cycle approach to risk management. mCom ONE supports safety conformance for adaptive configurations, thereby paving the way for effective hazard management in the world of IoT.